Test Equipment
Testing is a very important aspect of every repair and overhaul we carry out and every stage is individually tested as work progresses. This is followed by comprehensive testing of the completed magneto or dynamo when the work is completed. This page shows some of our specialist test equipment.
The Octopus Electrical Test Bench
Dating from the early 1950s, this test bench, overhauled by ourselves, allows complete testing of all rotating electrical and ignition components to be carried out with ease.
The picture to the right shows a dynamo being tested.
Below, a crankshaft mounted dynamo is being tested with the help of our universal adaptor plate.
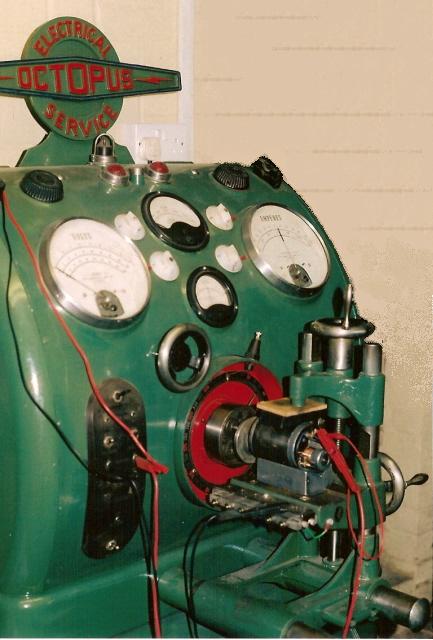
When testing dynamos on the Octopus Test Bench, the variables and configuration for the dynamo under test are selected on this test box, mounted adjacent to the test bench.
When the dynamo is being tested as a generator, the test load is applied by switching on any combination of these bulbs which vary from 6v, 5W to 12v, 55W. If needed, higher loads are added via the sockets in the centre.
This picture shows a twin cylinder magneto being tested - note the sparks on the degree ring which allows the cam spacings to be checked dynamically. Static checking is shown on the V Twin Magnetos
page in the Technical
section.
Pressure Test Chamber
Spark plugs are, of course, required to work under pressure in the combustion chamber. Normally, we test our magnetos at atmospheric pressure but compensate for the easier conditions by using a larger test gap. However if testing under pressure is necessary, we use this pressure chamber connected to the air line to give the required pressure. Note the safety gap - there is no point in testing with increasing pressure to such an extent that the coil's insulation is damaged!
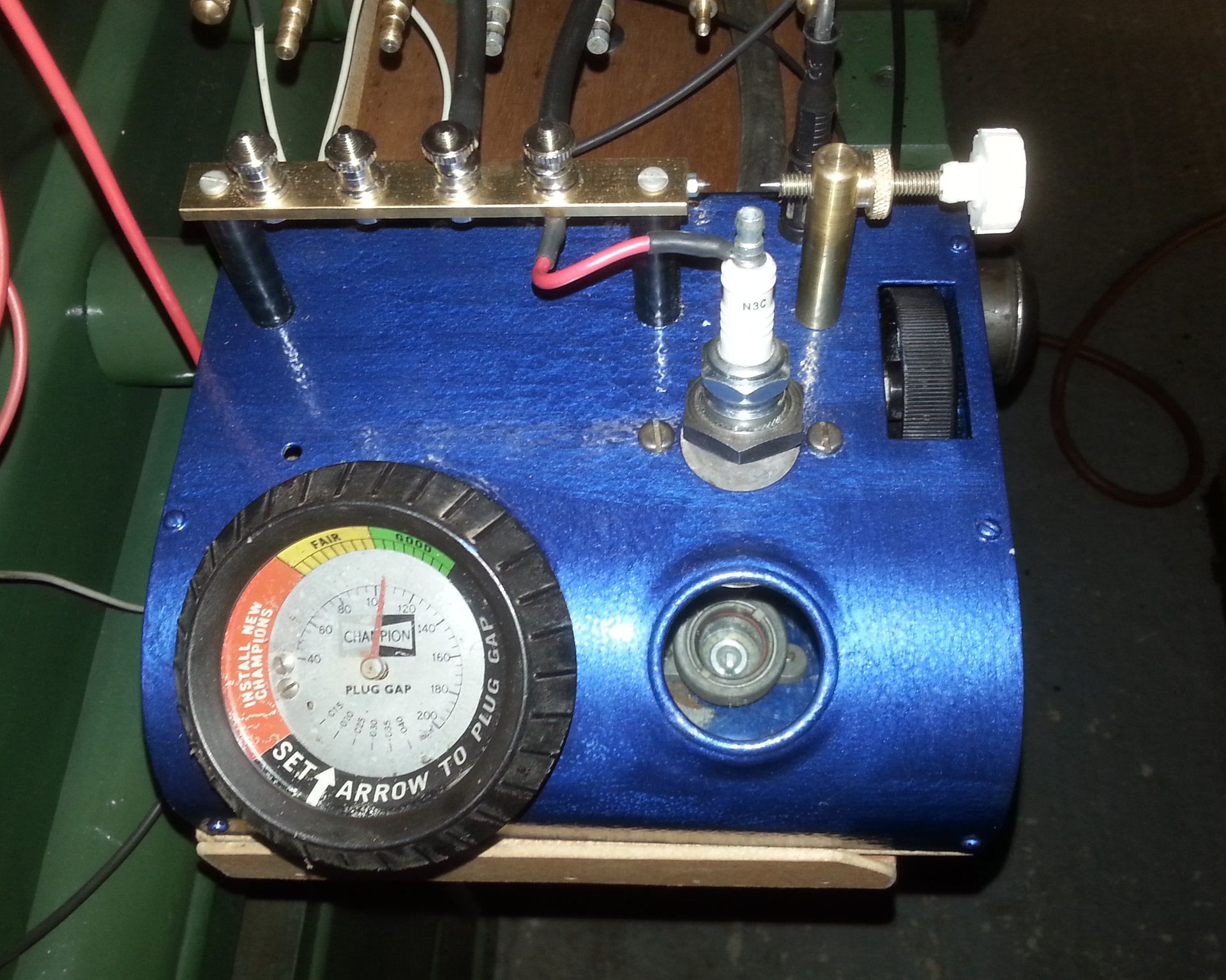
Spark gaps
On the Octopus Electrical Test Bench, we use annular test gaps. These are ideal for long term testing for up to six cylinder magnetos.
These adjustable gaps serve three purposes. They:
1: allow us to vary the test parameters when necessary.
2: add to the capacity of the Octopus Test Bench's annular test gaps for testing up to 14 cylinder magnetos.
3: can be moved along the rod to alter the spacing between the test gaps - needed when testing a bunch of HT leads when they are housed in a metal tube, each lead exiting adjacent to it's spark plug on the engine.
Holding the HT lead a set distance from the magneto body and then trying to turn the magneto to check for a spark is NOT a good idea. The size of the gap will almost certainly change as the magneto is turned - if it gets too big the spark will have nowhere to go so may damage the insulation in the magneto. We use a variety of hand held test gaps to suit particular test situations. These allow a consistent test gap to be safely used.
Armature Testers
We usually test dynamo armatures on a growler - this one came via eBay. All we had to do was clean it up, replace the perished cables, and give it a coat of paint! Instructions on how to use the growler can be found on the Using the Growler
page in the Workshop
section.
An alternative, shown below, is a Kenyon DC Armature Tester manufactured in our workshop. The design was based on the theory provided in an article on testing dc armatures found in a 1932 issue of 'Automobile Electricity' - a technical trade magazine.
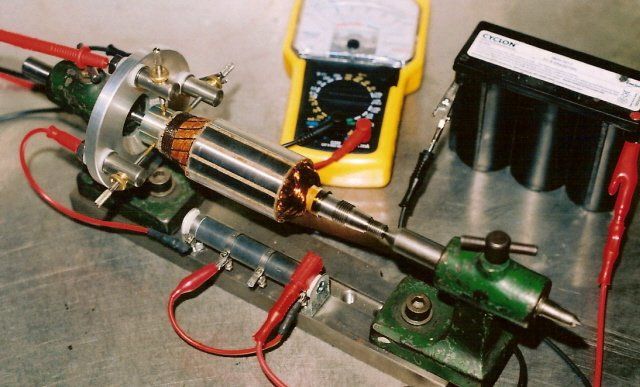
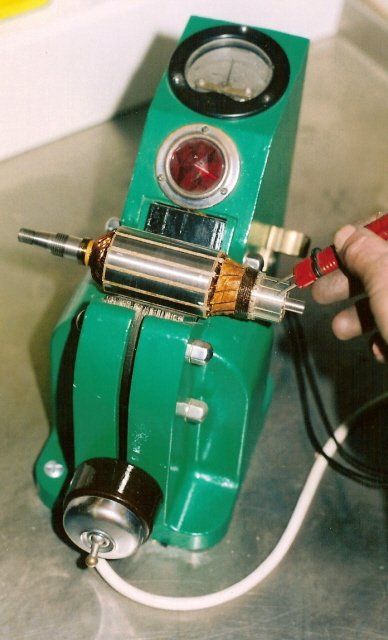
High Voltage Coil Tester
We made this piece of test equipment by modifying a rotating magnet Scintilla magneto. The picture shows an original coil with failed insulation - a short-circuiting spark can be clearly seen.
Below on the left - all rewound armatures are tested here as soon as they come out of the oven following the VPI process so that they are tested hot. Below on the right - all assembled armatures complete with condenser and slip ring fitted are tested too. The wire roving probe is used to check for any localised insulation leakage.
High Voltage Insulation Tester
This high voltage spark generator was modified by us to enable insulation testing of bakelite or plastic components including pickups, slip rings, rotor arms and distributor caps. If the component passes, we put it in the oven and heat it to about 65-70°C and then test again. Problems are more likely to show up at elevated temperatures.
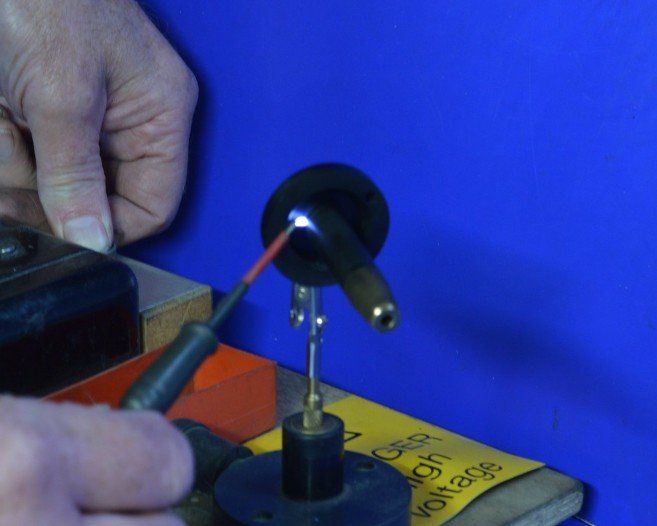
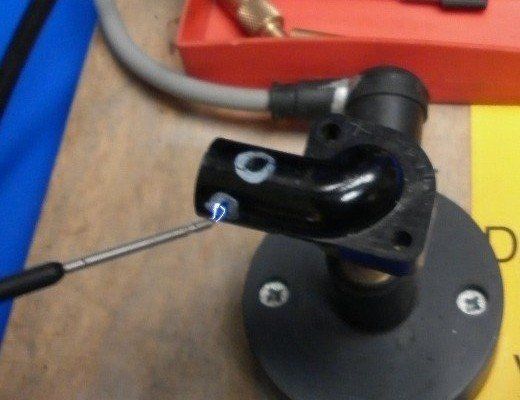
Stroboscopes
Two stroboscopes here, the gun type clips onto an HT lead and is used to dynamically check built in advance and retard units on magnetos. The other has an independent timer circuit which is ideal for making moving objects 'stand still'. One example of it's use is shown on the Points Bounce page in the Technical
section.
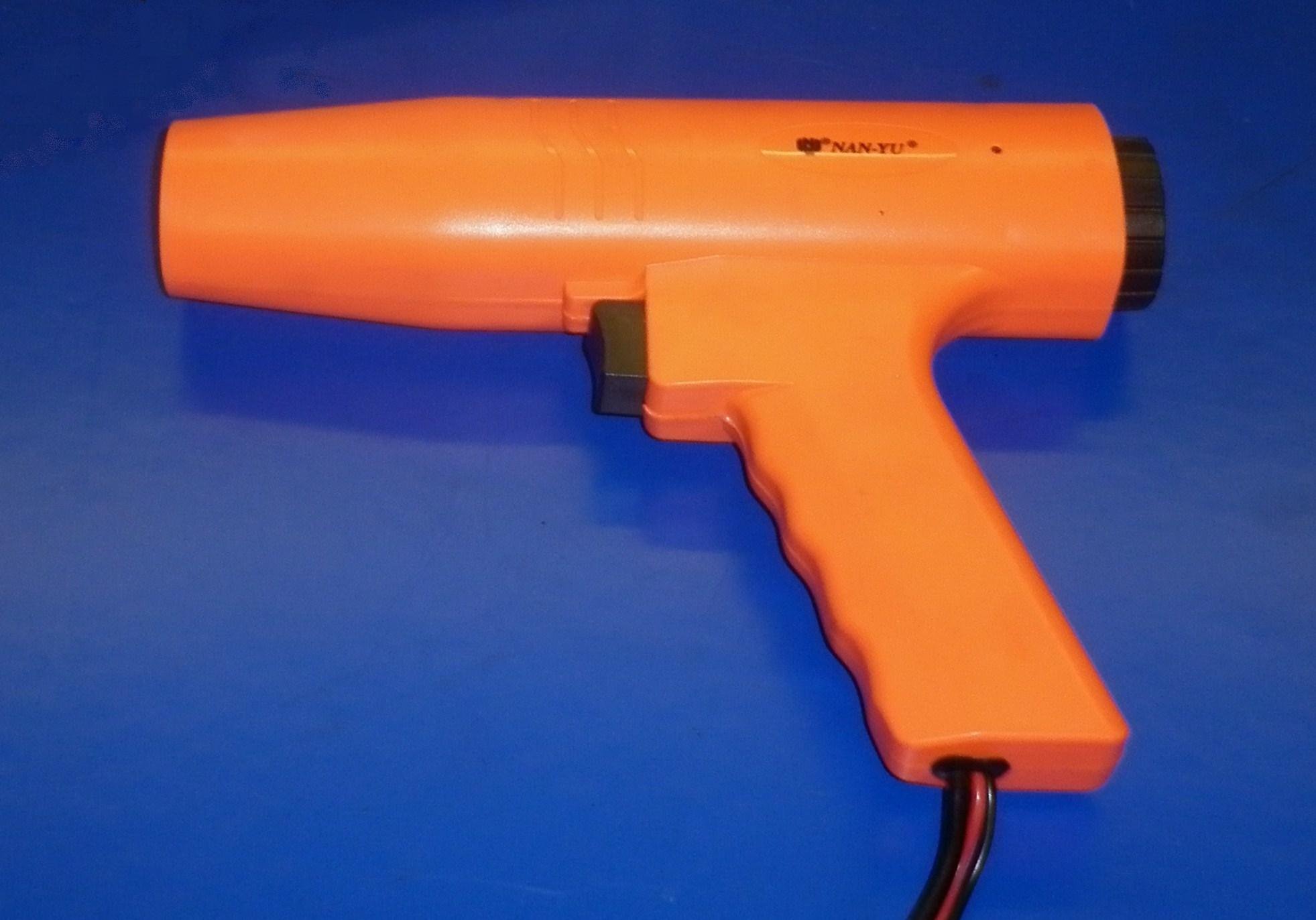
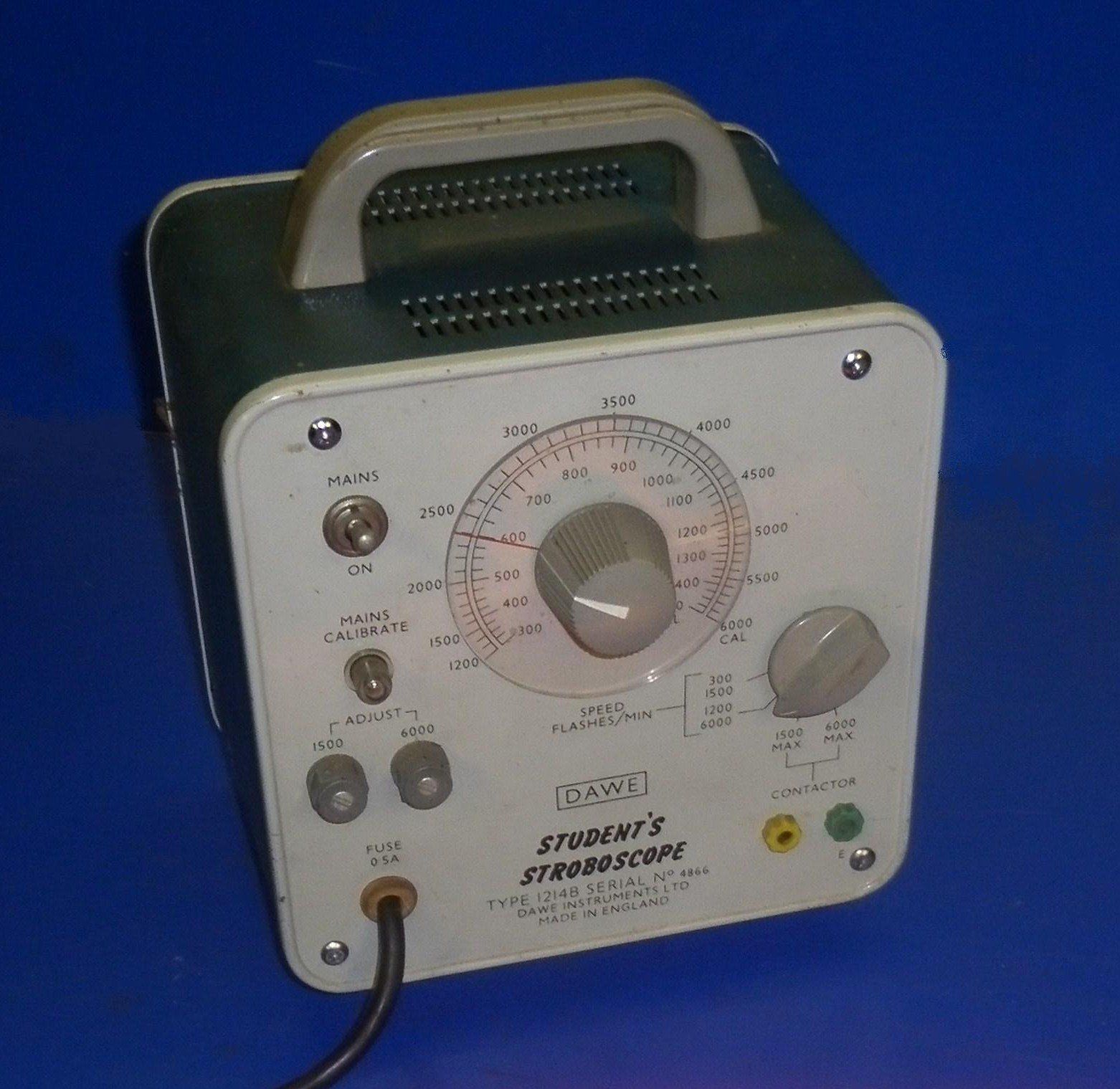
Spring Strength Tester
We often have to make springs, usually for magneto pick up brushes or dynamo brushes. We made this tool to be able to check the spring properties to make sure we got them right!
Electronic Voltage Regulator Tester
We always buy in electronic regulators
so don't do a lot of work with them other than to test them when a dynamo is suspected of not working. We made this test box so that we could do a quick and conclusive test using just a bench power supply to apply an adjustable voltage to emulate a dynamo output.
HT Polarity Tester
We made this electronic tester to check the polarity of the HT spark. More details on Spark Polarity
and why it is important can be found in the Technical section.
Field Coil Polarity Tester
A battery with a bulb to limit the current, can be used to pass a current through a field coil. A compass can then be used to determine the field coil polarity - especially useful when the dynamo has several field coils mounted in series as it allows the coil interconnections to be checked.
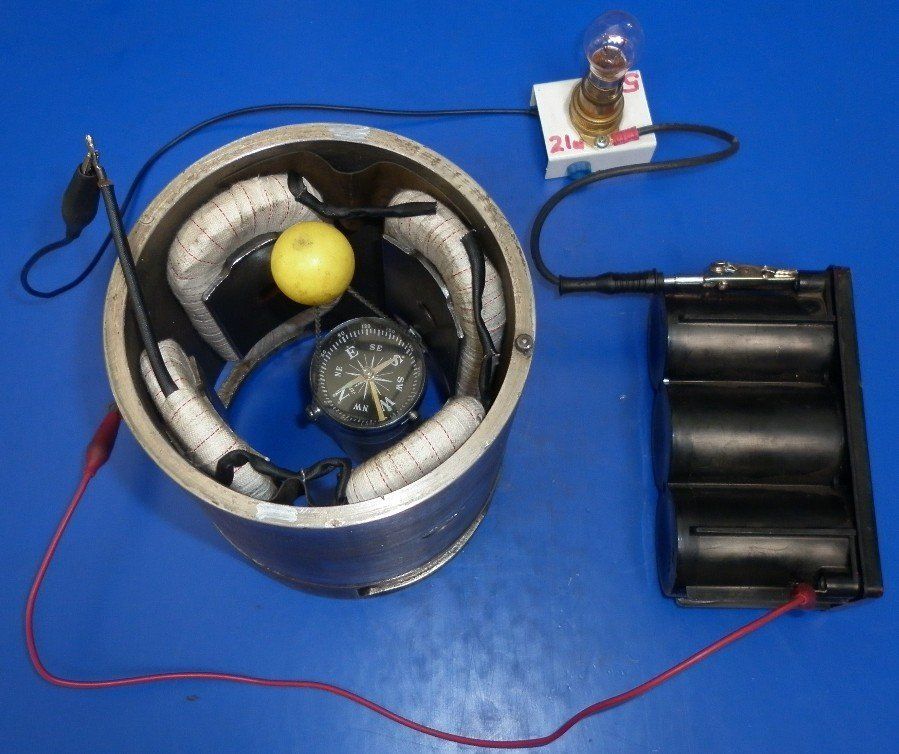
Coil Continuity Tester
We modified a Stanley knife by fitting a small buzzer circuit together with batteries inside the knife where the spare blades are usually housed. A small micro switch inside the knife automatically switches the circuit on and off as the blade is pushed in and out. The flying lead connects to one end of the winding and the blade itself, acting as the other terminal, is sharp enough to pierce the enamel coating on the wire to check for a continuous circuit.
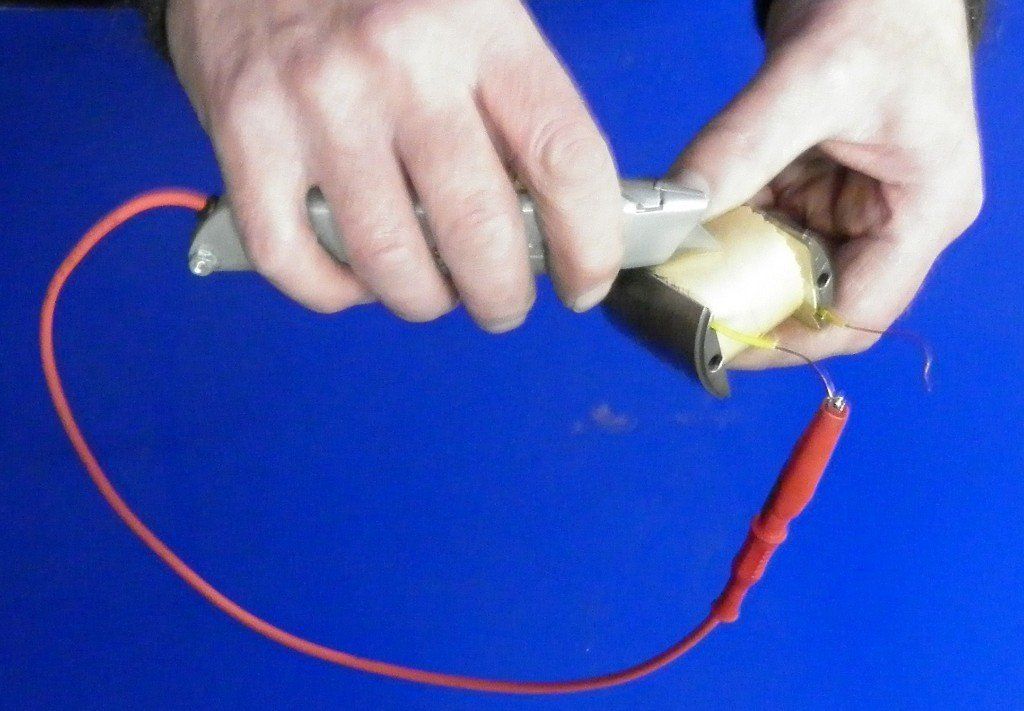
And finally....
Some standard 'off the shelf' test gear! Standard mechanical engineering test gear is used to check that re-assembled armatures are running true. Standard electrical test meters are used to check capacitance and insulation properties of condensers - we always test them after heating to 60-70°C. Full details of how we test capacitors are explained on our Condensers-practical
page in the Workshop
section.