Spark Test Gaps
As described on the Voltage at the Spark Plug
page, the size and shape of the gap which the spark is expected to jump has a big influence on the magnitude of the HT voltage required. When testing a magneto, here at The Magneto Guys, we have several different types of test gaps that we use:
Adjustable two point gap:
can be unstable and uncertain in it’s operation but even so, is a good way of checking for a spark. The size of the gap is easily and quickly adjusted.
This one is most commonly used for quick bench tests. The round base is fitted with small magnets to grip the metal bench top or the vice.
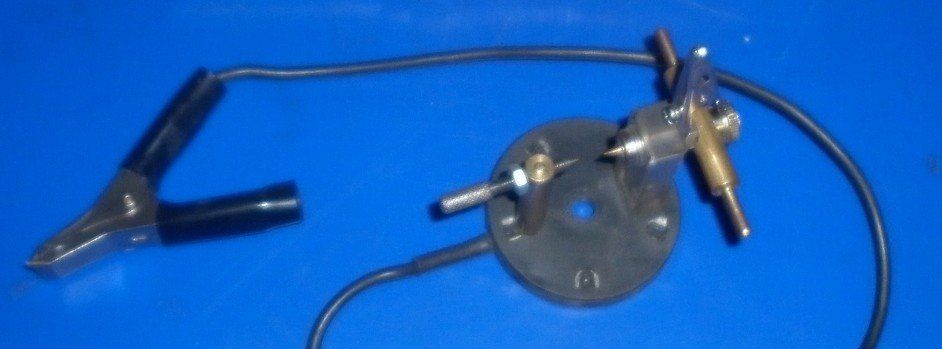
These are used when a magneto reassembly has reached the stage where it should be able to produce a spark. The spring loaded brush fitted to these testers can be used directly on a slip ring.
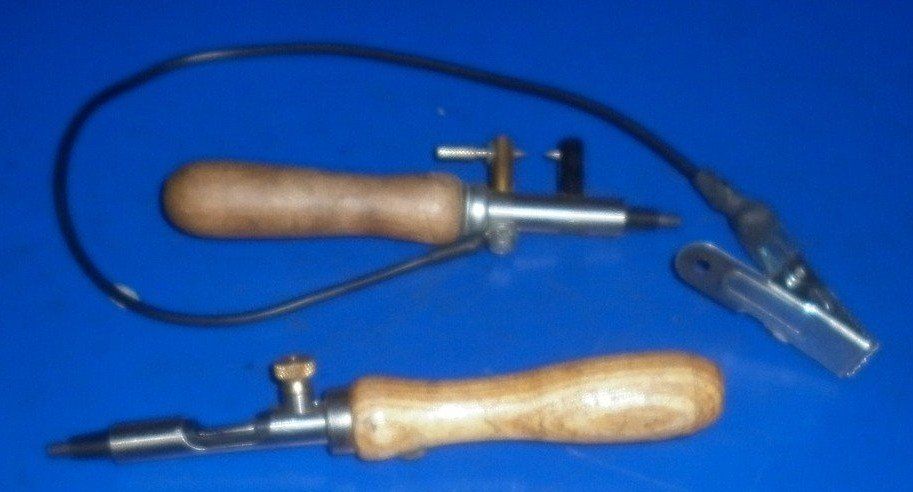
Here is part of a group of single point test gaps fitted to a common earth rod. Each individual test gap can be moved along the rod to adjust the spacing to suit individual setups.
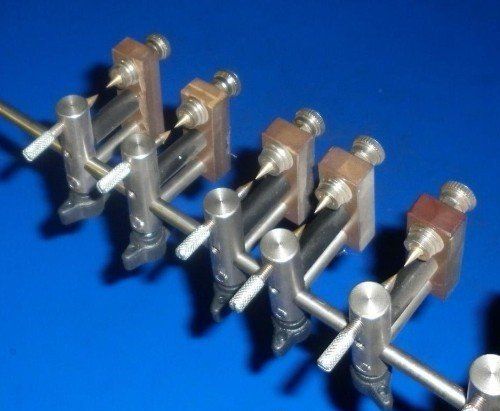
Annular gap: gives a more or less constant discharge voltage at all magneto speeds so this is the type we use for our long term running tests on the Octopus Electrical Test Bench.
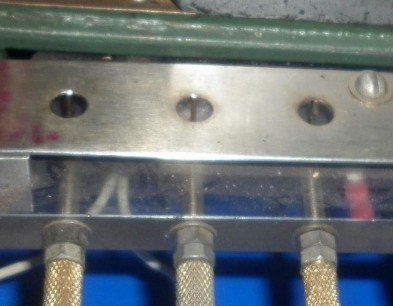
Rotary gap:
The spark jumps between the protractor ring and a pointer attached to the drive shaft. Useful for checking angles between sparks on twin cylinder magnetos especially those used on V twins.
There are other types of test gaps available:
Adjustable three point gap: Introducing a third point makes the voltage required to jump the spark gap a much more stable and consistent figure. This makes the three point gap technically better than the two point test gaps shown above. Rapid wearing of the points and the need for careful adjustment of the third point are disadvantages. We don't use these very often.
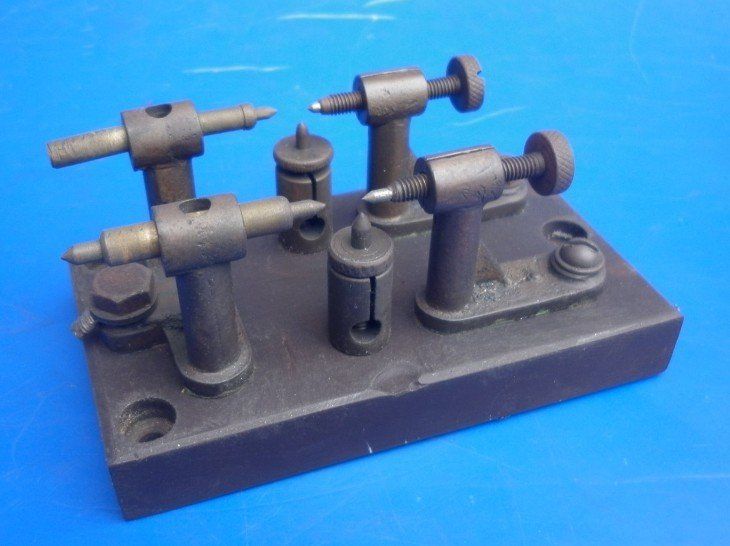
Spherical gap: According to the Physics text books, a calibrated spherical spark gap will break down at a highly repeatable voltage and can provide a voltage measurement without any electronics or voltage dividers, to an accuracy of about 3%. Here at The Magneto Guys, we are not usually interested in the actual value of the HT voltage we are getting, just so long as we are getting a spark! Sorry, no picture of these - we don't have any! Just imagine an arrangement identical to the single point test gap shown above but with a ball bearing on each of the points.
All of these gaps are of course at atmospheric pressure which is not a true representation of the conditions inside the cylinder where the spark is required towards the end of the compression stroke and therefore under pressure. We compensate for this by making the test gaps much larger than the normal spark plug gap.
We also have a test rig which tests the spark across a normal spark plug gap under pressure. The conversion factor for compression ratio to psi is generally agreed to be 14.7psi – this figure makes a number of assumptions such as all valves closed at the very start of the compression stroke and no leakage past valves or piston rings any of which would reduce the actual pressure. However, using this conversion factor assumes ‘worst case’ figures so makes a good test figure. So, a compression ratio of 10:1 equates to approximately 150psi.
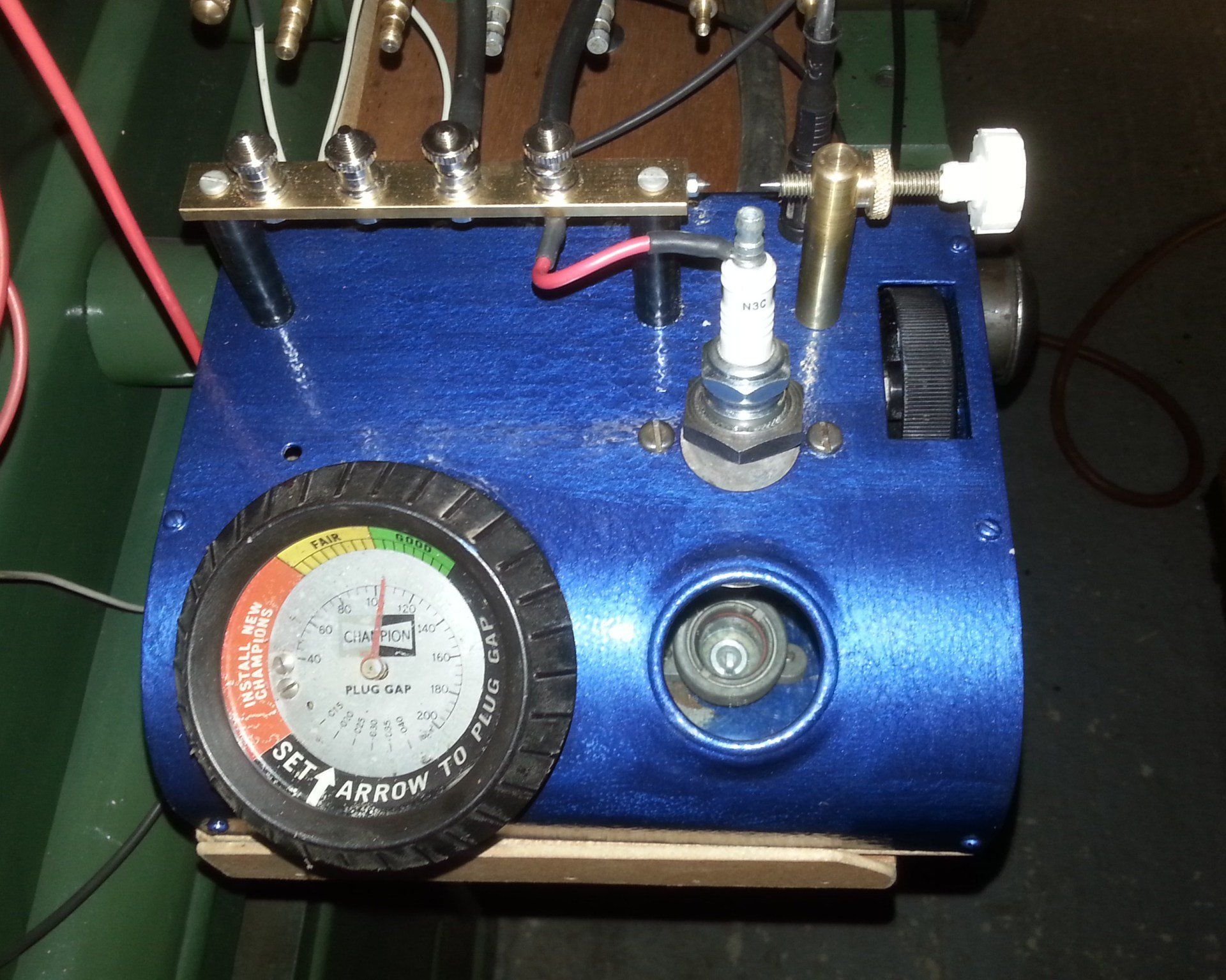
When this picture was taken, a twin magneto was being tested at 125psi. The spark plug is a standard Champion N3 plug with the gap set to 0.020”. This test rig could be used to investigate using both increased gap and increasing pressure but it is important to remember that as these two factors increase, the breakdown voltage will increase proportionately. This puts an increasing strain on the magneto’s insulation in both the coil winding and the pickup/slip ring HT path. It is undesirable to ‘test to destruction’ so the rig has a safety gap which is set to 12mm – this ensures that if the pressure is increased to such an extent that the spark plug gap stops sparking, there is a path for the high voltage to discharge. Without that safety gap, it is likely that the coil insulation will be overloaded and permanent damage caused. There are in fact, two safety gaps fitted as standard on the magneto itself which are much smaller than the 12mm safety gap on the test rig. They would almost certainly come into use before the larger safety gap on this test rig. Actually, this particular magneto was to be fitted to an engine with a compression ratio of 5.44:1 so checking for a good spark at about 80psi would have been enough.
And finally, here is a simple easily made test gap. It's quite well known that seeing a spark with the plug held against the cylinder doesn't prove it will work when replaced in the cylinder. This is because, against the cylinder, the plug is at atmospheric pressure whereas inside the cylinder it is under compression so at a much higher pressure. A good method is to use a modified spark plug for the test. Just break the earth electrode off of the plug and test as before. The increased distance that the spark needs to jump will compensate for the lower pressure outside the cylinder so provides a more reliable result. Don't put this test plug in the engine though!
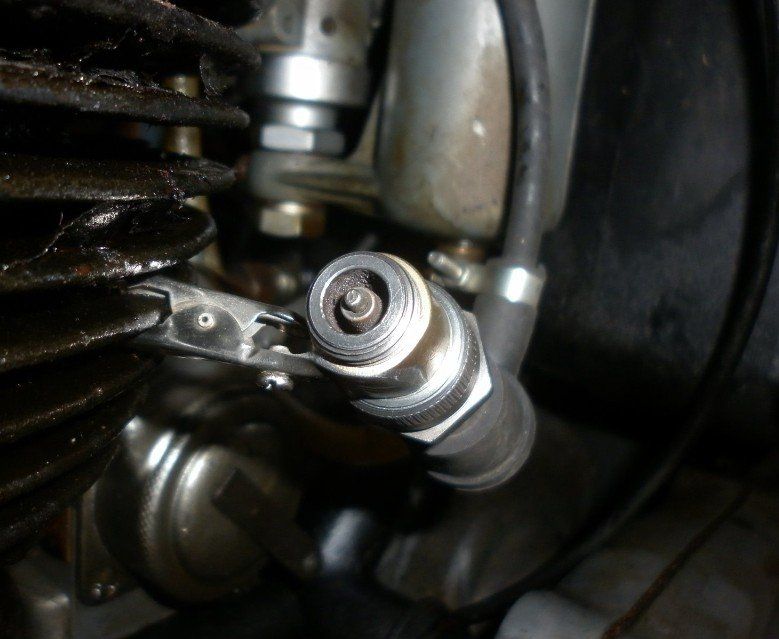